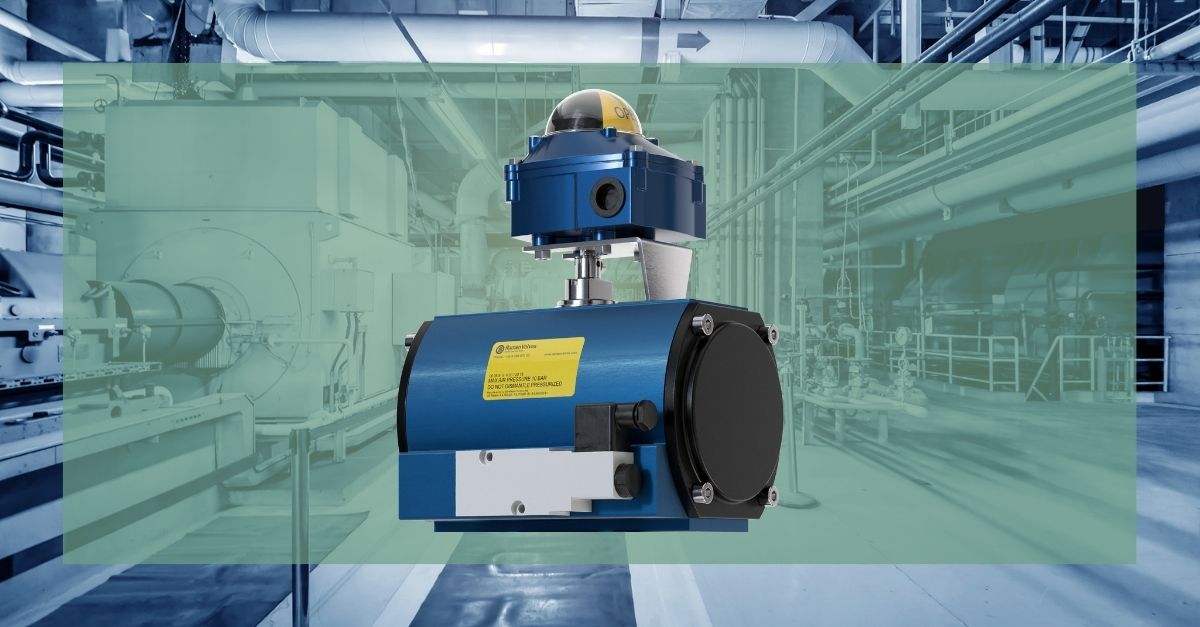
Ramén Valves, 12 December
What to consider when choosing automation for ON/OFF valves
When choosing automation for ON/OFF valves, there are several important factors to consider to ensure that the selected automation solution meets your operational requirements and optimizes your system’s efficiency.
Here are some key considerations:
Valve Type and Size:
Understand the type (ball, gate, butterfly, etc.) and size of the valves you need to automate. Different valve types and sizes may require different automation mechanisms and actuator sizes.
Application and Industry:
Consider the specific application and industry in which the valves will be used. Different industries have varying requirements for precision, reliability, and safety. Industries like oil and gas, water treatment, pharmaceuticals, and manufacturing may have specific compliance and regulatory requirements.
Automation Mechanism:
Choose the appropriate automation mechanism, such as pneumatic, hydraulic, electric, or electro-mechanical actuators. Each type has its own advantages and disadvantages in terms of speed, control, reliability, and maintenance requirements.
Control System Compatibility:
Ensure that the chosen automation solution is compatible with your existing control system or SCADA (Supervisory Control and Data Acquisition) system. Compatibility is crucial for seamless integration and effective control.
Control Speed and Response Time:
Consider the required speed and response time for opening and closing the valve. Some applications may require rapid response, while others may prioritize gradual and controlled movements.
Safety and Redundancy:
Evaluate the safety requirements of your system. In critical applications, redundant or fail-safe automation systems might be necessary to prevent accidents or process failures.
Environmental Conditions:
Assess the environmental conditions in which the valves will operate. Factors like temperature, humidity, corrosive substances, and hazardous atmospheres can influence the choice of automation components and materials.
Maintenance and Reliability:
Consider the maintenance requirements of the automation system. Choose components that are durable and require minimal maintenance to ensure reliable and efficient operation over time.
Energy Efficiency:
Evaluate the energy consumption of the automation solution. Opt for energy-efficient actuators and control systems to minimize operational costs.
Remote Control and Monitoring:
If necessary, consider whether the automation system needs to support remote control and monitoring. This is particularly important for distributed systems or systems located in remote areas.
Integration with Existing Infrastructure:
Ensure that the chosen automation solution can be easily integrated with your existing infrastructure without significant modifications.
Lifecycle Costs:
Take into account the initial investment, installation, operating, and maintenance costs of the automation solution. Sometimes, a slightly higher upfront cost can lead to significant savings over the system’s lifecycle.
Supplier Reputation and Support:
Choose a reputable supplier or manufacturer that offers good customer support and reliable after-sales service. This can be crucial in case of technical issues or the need for spare parts.
Future Scalability:
Consider whether the automation solution can be easily expanded or adapted to accommodate future changes or expansions in your system.
Training and Expertise:
Ensure that your team has the necessary training and expertise to operate and maintain the chosen automation system effectively.
By carefully considering these factors and possibly consulting with automation experts, you can make an informed decision that aligns with your operational needs and long-term goals.