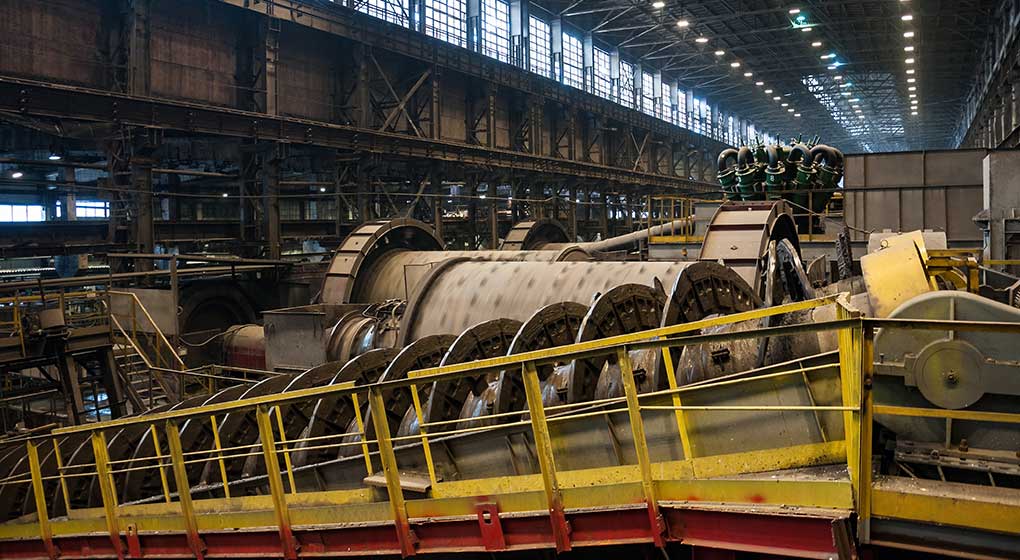
Mines and mineral processing, Ramén Valves, 25 January
How to choose the right ball sector valves for enrichment plant processes
The enrichment of metals and minerals mined in a mine places special demands on the equipment. This applies not least to the valves that regulate and isolate media in the plant. Using the wrong valves increases the risk of costly downtime, accidents and environmentally harmful emissions. Not to mention shorter product service life and expensive maintenance.
So how do you come up with a good solution?
The right valves are essential for efficient and safe mining
Mineral processing is hard on the equipment used in mining processing. But choosing quality products is not enough, they must be the right products for the purpose. Not least regulating valves come in lots of variants and sizes, and one size does not fit all.
Avoid the trap of resorting to old input data used for previous installations – it may well be out of date. Nor is it a good idea to blindly rely on the supplier identifying the problems.
If you perform technical investigations and help companies in the mining industry to optimise their processes, you would be well advised to ensure for yourself that the supplier has the right data. Find out which process characteristics are to be achieved, and specify them in the documentation. Always ensure with the client that the input data is correct and up-to-date. Old input data can cause major problems in retrospect when components such as valves are dimensioned incorrectly by the supplier.
Choose a product based on use
When choosing valves, the most important thing is to work on the basis of the relevant media and applications, i.e. what the valve is to control and what is to be achieved in the process, such as a certain flow, pressure, level, temperature or other aspect.
Common media include:
- Slurry, a mixture of sand, minerals and other materials that are processed in various stages to produce end products such as gold, silver, iron or zinc
- Water, e.g. process water or flushing water
- Chemicals added to purify or extract minerals
- Gas, such as natural gas, oxygen, nitrogen, hydrogen or other industrial gases
In an enrichment plant for iron ore, the ore is finely crushed, impurities are removed and the iron content is increased. To access and remove impurities, the ore is ground to a fine concentrate and mixed with water to form a slurry.
Some common applications in the mining industry are the control of lime water, grinding water and make-up water. Other applications include managing water flow to and from separators, water recycling, dewatering or sand pumping. Each application makes its own specific demands on the valves.
A regulating valve must be sized and optimised for the job it is supposed to do, i.e. for the media it is supposed to regulate. Any processes it is subjected to during start-up, cleaning or shutdown must be taken into account. Valves can regulate different media, but they can also be used to dose chemicals or water, for example, in order to achieve optimal process characteristics. It is important in this case to ensure it is adapted to the media and volume to be dosed.
Having too few chemicals may impair process performance and cause failure of the product made by the plant.
Having too many chemicals is bad for the environment and wears out the equipment, resulting in shorter service intervals. The fact that chemicals are often expensive also increases the cost of production.
The materials in the valves also impact on sustainability. Some materials are corroded by the chemicals – the valve simply rusts away. Corrosive, acidic and explosive chemicals have specific material requirements. The particles wear down the valves, causing erosion in valves coated with certain coatings such as ceramic. Rubber-lined products are available that are designed to cope with the slurry by repelling the particles from the surface.
Installation and maintenance are also part of the use of the product. How difficult is it to maintain and replace the products?
Correctly sized valves of the right quality dramatically increase service intervals. It is a major advantage if they are also easy to service and do not require complicated interventions such as hose changes.
Sizing and product selection – this is where things have to be right
Sizing a regulating valve correctly is crucial for a process to run efficiently and without failures. The supplier makes calculations to ensure a cost-effective, reliable and sustainable valve solution. These are based on your input, which means that complete and accurate tender documentation is crucial.
The most important factors for correct sizing are:
- Media
- Flow – min, normal, max
- Temperature of media
- Inlet pressure
- Outlet pressure or backpressure, i.e. pressure drop across the valve
Other parameters to consider:
- Pressure drop when valve is closed
- Density, viscosity, concentration and the presence of abrasive particles
- Pipe size and material
- Suitable materials for parts in contact with media
- Any requests for actuators, positioners or accessories such as solenoid valves, limit switches or air filter regulators
The physical dimensions of the solution, how much space the valve requires in the installation, are also important. A compact small valve solution makes installation and maintenance easier than a solution requiring a lot of space.
The material does of course need to match the medium and the application. If the valve is to withstand a high mechanical load, such as being opened and closed many times, this needs to be taken into account when sizing the solution. Also check that it is CE-marked according to the Pressure Equipment Directive.
Choosing products wisely is very much about finding the right quality level. For example, using stainless steel or unnecessarily large valves when they are not needed is an unnecessarily major investment. On the other hand, technology that is too simple or choosing cheap materials often leads to demanding maintenance work, and expensive production failures in a worst-case scenario. Regardless of the technical level, the supplier must have test-pressurised the products and issued an Inspection & Test Plan, ITP, or functional certificate. While you are asking for this, you can also ask to see the calculation data as well, which shows what input data was used and what choices the supplier made.
If the valves are to be connected to a digital communication system such as Profibus, they need to support the industry protocol applicable to the plant in order to work.
Look at the life cycle cost
Cheap products can turn out expensive. Going for the lowest unit price is a risky strategy as it is often synonymous with inferior materials and construction. Products break or wear out more quickly. A malfunctioning or leaking valve compromises safety and production and increases maintenance costs. The purchase price is just the tip of the iceberg. To be able to propose economically sustainable solutions for the mining industry, you need to take into account the total cost over time, known as the Total Cost of Ownership, TCO.
Some factors to consider that contribute to the overall cost include:
- Service life
- Maintenance intervals
- Spare parts requirements
- Need for cleaning
- Fault rate
- Wear and tear
- Harm to the environment, people and equipment
- Production losses and delays
- Energy consumption
- Consumption of oil and other lubricants
The valves are a small part of the enrichment of minerals and metals, but a very important part nonetheless. We hope you now have a better understanding of what to consider when designing solutions for a mining plant involving valves.
If you would like to know more about how to ensure the reliability of your mining production, please download our guide “Valves in mining enrichment – how to ensure operation (and avoid unplanned downtime)” ⇓
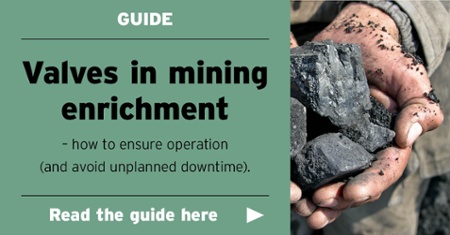
If you have any questions about which valve solution would be suitable for a particular plant, please contact us.
Do you want to know more about our Ramén KSG rubber lined valve, specially designed for the mining industry? Read here.
Ramén Valves has been a valued partner to the mining industry for 40 years. We supply valve solutions for applications commonly involving abrasive media.