ON/OFF valve solution for a fly ash application in a heat & power plant
A heat and power plant in Stockholm had for a period of time experienced difficulties with the valves in one of their applications that involved fly ash. Ramén Valves offered them an improved
ON/OFF valve solution that helped to withstand the harsh media.
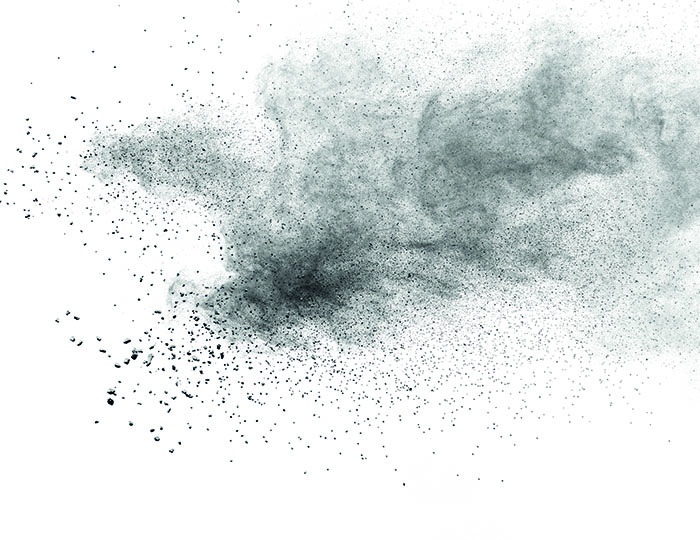
The case in short
Customer: Heat and power plant, Stockholm, Sweden
Temperature: 150-250°C
Media: Fly ash carried by air. Ash is created by the combustion of wood pellets.
Pressure: 6-7 barg
Function: ON/OFF
Previous solution used by the customer: Standard butterfly valves and ball valves that could only withstand the media for a few weeks before they needed to be replaced.
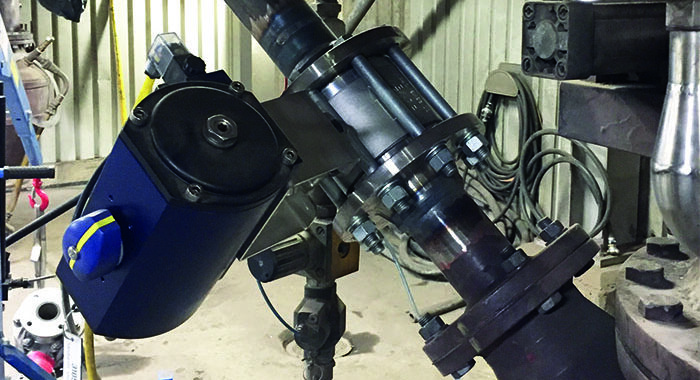
Our solution
A Ramén KS Ball Sector Valve model 1E with an innertube. The ball sector and the seat holding ring are made from stainless steel treated with SuperExpanite®, which provides a high hardness and protection from abrasion. The model 1E is a unique feature on the market providing a deep stellite seat that offer an extra protection on the seat holding ring. The inner tube is made from stainless steel and directs the flow from the inlet of the valve directly to the outlet of the valve, protecting the body from any possible abrasion.
Result: After one year of operation, all parts in contact with the media have not faced any abrasion and the valve still operates successfully with the same tightness as it originally did.
Ramén Ball Sector valve with an inner tube
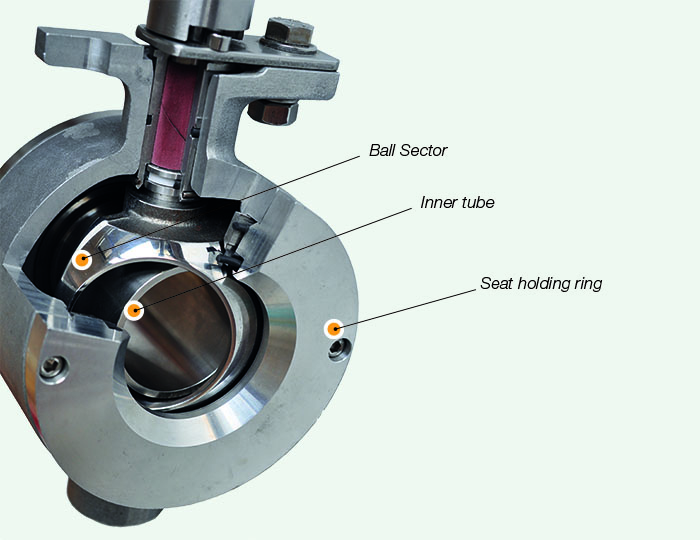
The end of the added inner tube lies close to the inner diameter of the ball sector. This prevents the flow from the abrasive media to get in contact with the wetted parts (seat and ball sector). This also prevents the cavity of the valve to entrap media when turning from opened to closed position.
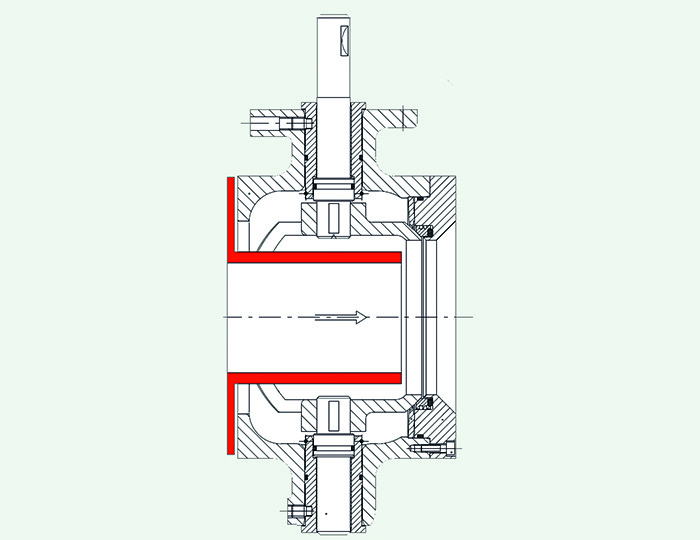
The sketch shows how the inner tube is placed inside the valve body.
Contact us
Use the form to contact us.